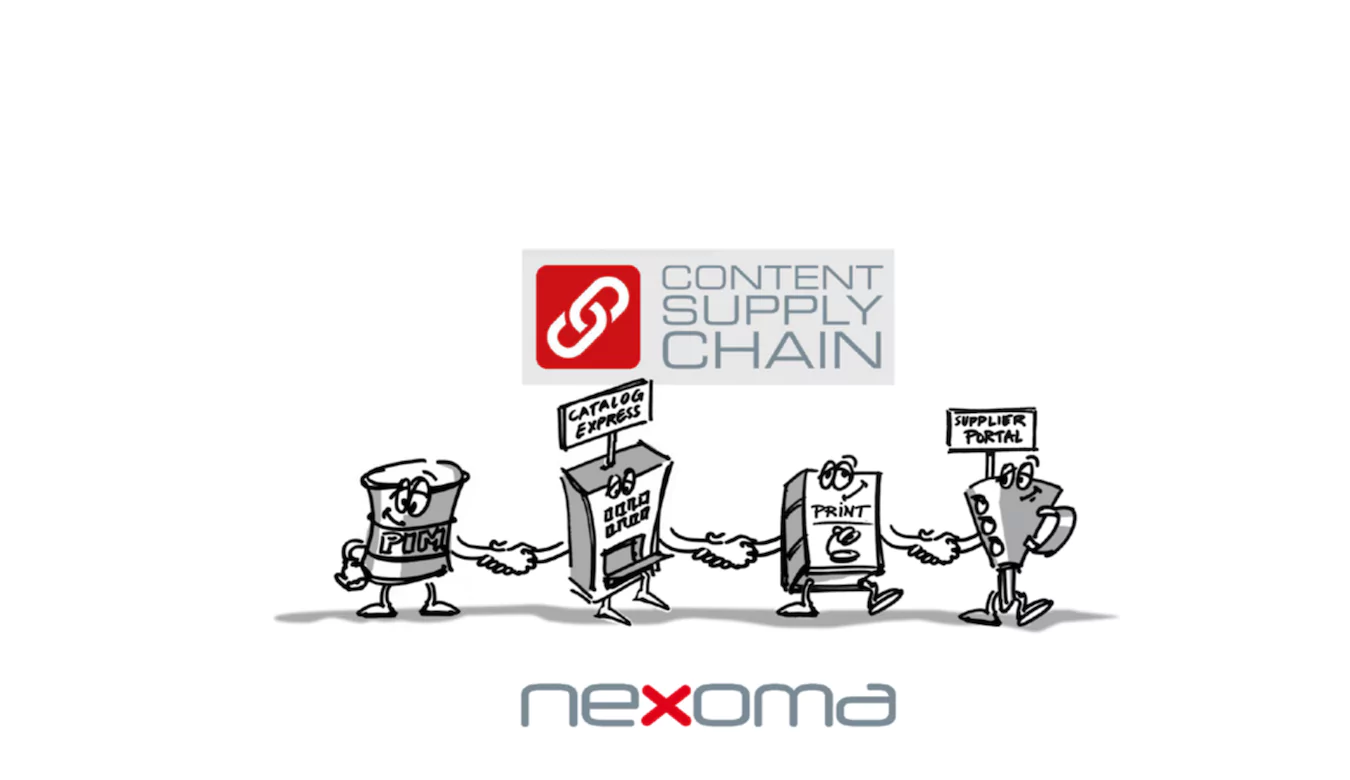
23 Aug eBusiness concept: Content Supply Chain
eBusiness concept: Content Supply Chain
What is meant by supply chain?
“nexoma” focuses on the processes of the associated product data and -information with “Content Supply Chain“. With the help of Content Supply Chain, the corresponding processes can be presented in a comprehensible way for all employees across departments and companies.
The content supply chain is derived from the classic supply chain, which covers the entire process from the production of raw materials to the arrival of products and services at the end user. Starting with the procurement of raw materials for manufacturing, the production as well as the distribution of the products are part of the classic supply chain. Since the products increase in value in the course of processing, this is also referred to as a value chain.
But also product data and information pass through the most diverse areas in the supply- and value chain of the products, in which they are required and used. Therefore, the content supply chain as a concept of eBusiness can be divided into 3 process steps: Data procurement, data refinement and data distribution.
Data procurement and Data Onboarding
For every product, there are countless data and information already at the beginning in research and development or from the manufacturing supplier. This includes, for example, product texts, technical information, logistics data, but also assets such as data sheets, images, videos and also prices. In addition, classifications, data standards, and also customer and market requirements determine what product information is expected.
Before the product data can even reach the company’s own systems, the data exchange between manufacturer/supplier and data recipient must take place. This is often very complex, as the data supplied often has a wide variety of formats and files, such as BMEcat, EXCEL or CSV, and different classifications, such as ETIM or ECLASS. Often, the data recipients then lack the possibility to process the supplied data at all.
Checking, preparing and importing this data into the existing systems (e.g. PIM or ERP) is very laborious, time-consuming and cost-intensive.
Supplier-Portal from nexoma takes over these steps automatically. In the first step, the supplier onboarding, the product data of the supplier as well as the company data and contact persons are recorded. Subsequently (second step), the data quality check takes place. Here, the data is checked for both quality and quantity. The supplier receives direct feedback as to which data needs to be revised or is still missing. In the final step, the recipient can then select which data should be transferred to his own system. For this purpose, the data is put into the right structure and format, which the own systems can import.
Data refinement and product data management
In order to be able to enter, manage and prepare all this information efficiently and in a resource-saving manner, PIM systems such as Pimcore are used. These collect the data and information from different sources and process them. Here, all product data are saved consistently, completely and in high quality and can be processed further. A PIM system thus represents the single point of truth, i.e. the central point where the criteria for the quality and quantity of article and product data are met.
This is because the information maintained there are crucial for eCommerce, but also for all other downstream stages of the content supply chain. This can include keywords for marketplaces, classifications for industry standards, pure marketing content such as catalogs, or price lists for defined customers.
Data distribution and product data syndication
Every customer or system has different requirements for data, thats why it is important to have a custom-fit and individual preparation. At this point CatalogExpress comes into play. CatalogExpress collects item and product data, as well as prices and inventory data, from a variety of source systems such as PIM or ERP and prepares them in the required format automatically. At the push of a button, individual Excel, BMEcat or CSV files can be created for electronic catalogs, taking into account classifications such as ETIM or ECLASS. Likewise, the marketplace connection and data provision to customers can be automated and time-controlled.
But data aren’t needed online only, but also in print and publishing media. Although products are increasingly sold online these days, when they are used in traditional media, this is done in a much more targeted manner. Customers are only shown products they are really interested in.
Thanks to print automation, the required data are pulled from PIM, ERP or DAM systems. This ensures that catalogs, flyers and brochures are always supplied with the latest information and data on the respective products. This saves both production time and costs and also increases the chances of better market placement.
You can also find an exciting video about our content supply chain on our Youtube channel!