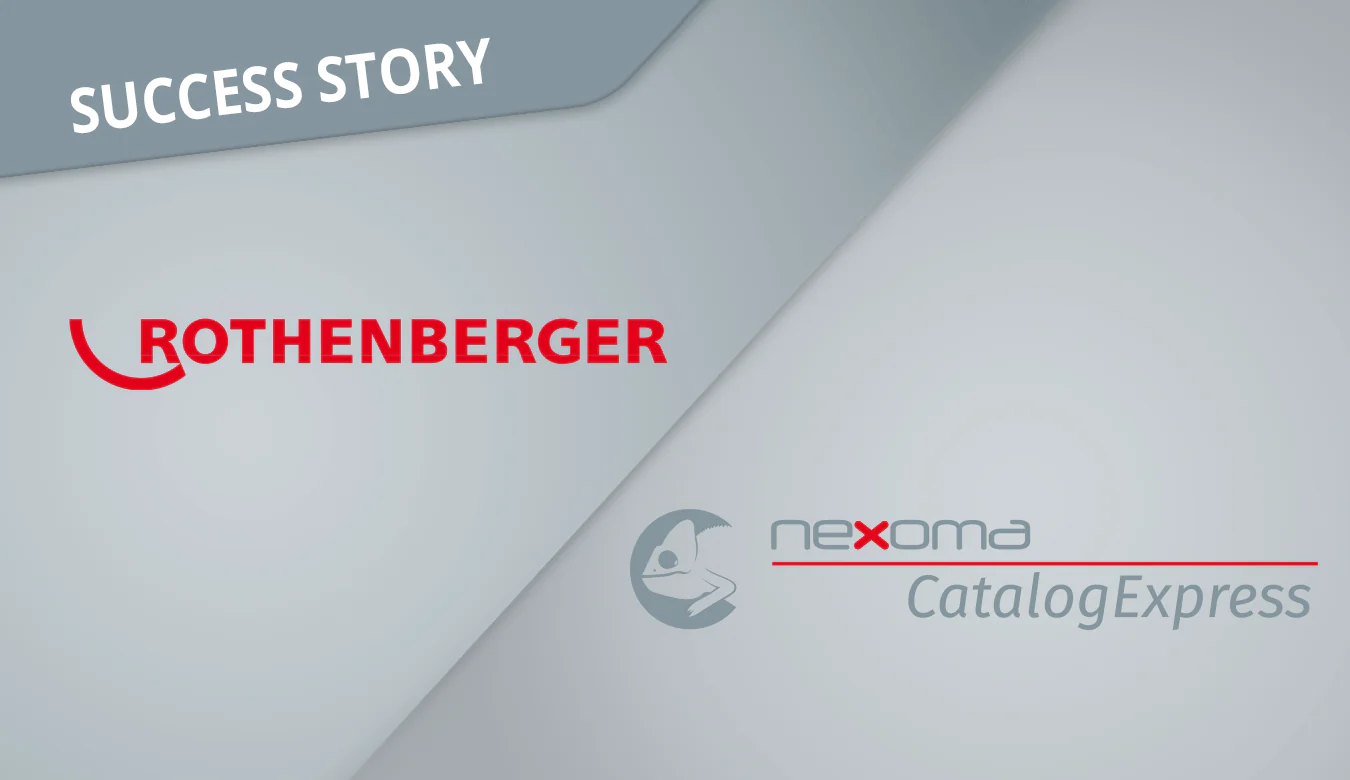
28 Jun How ROTHENBERGER Increases Customer Satisfaction through Data Syndication with CatalogExpress
Initial Situation
ROTHENBERGER has to handle many different data requirements, some of which come from various countries. These include template-based EXCEL files, CSV, and FAB-DIS files, as well as highly customized BMEcat catalogs, which often involve numerous special UDX requirements. For example, some customers require image data to be provided as URLs, while documents need to be sent physically. Additionally, there are increasing requests from other countries for specific data exports.
Recognizing the necessity of effective product data management, ROTHENBERGER implemented the Contentserv PIM system at an early stage. The company also established a Product Data Management department within their marketing team, which developed a content definition guideline. This guideline precisely describes how each product attribute must be maintained and includes classifications (e.g., ETIM) and various customer or data standard requirements.
The tool and machine manufacturer regularly optimizes its product data, ensuring a very high level of data quality from the outset.
This continuous optimization is supposed be quickly reflected to customers and data recipients. In particular, ROTHENBERGER aimed to respond more rapidly to their growing data requirements.
ROTHENBERGER’s goal is to continuously increase the satisfaction of data recipients and further optimize processes in their data syndication.
Objective
Therefore, ROTHENBERGER sought a solution to deliver data to customers faster and more efficiently. They found the software solution CatalogExpress by nexoma in Contentserv’s Marketstore, which can handle all their data requirements.
CatalogExpress stands out due to its role distribution. The ‘Manager’ role allows ROTHENBERGER’s Product Data Management team to handle the technical setup of the data. In the CatalogExpress data mapping process, product data is prepared for various target formats (BMEcat, FAB-DIS, CSV, and EXCEL). Additionally, the ‘Creator’ role allows the sales team to easily create and send electronic catalogs to customers without requiring technical background knowledge.
Based on these criteria, ROTHENBERGER ultimately decided to use CatalogExpress.
Solution
First, a priority list was created in collaboration with nexoma, detailing when specific product catalogs or data exports will be configured in CatalogExpress. This initial step was developed jointly, allowing ROTHENBERGER to become familiar with the system. In the future, ROTHENBERGER will generate the product data catalogs independently.
Due to ROTHENBERGER’s familiarity with the data requirements of their customers, dealers, and platforms, quick successes were achieved with CatalogExpress. The standard interface to Contentserv enables rapid import of product data into CatalogExpress. In the data mapping process, source attributes from the PIM system are linked to the target attributes.
The numerous mapping functions help further refine the data, making it easier to meet customer-specific requirements. For example, ROTHENBERGER can now convert technical data directly in CatalogExpress without needing to create additional fields in their PIM system.
The first data transformations and deliveries via CatalogExpress have already received positive feedback from customers. ROTHENBERGER can manually export product catalogs with CatalogExpress or provide them automatically. The latter option has already been set up for some customer catalogs. In the future, ROTHENBERGER plans to further expand automated and scheduled data delivery.
This enables electronic catalogs (such as BMEcat, FAB-DIS, EXCEL, CSV) to be delivered to customers in the best and simplest way.
With the help of CatalogExpress, ROTHENBERGER now achieves efficient data syndication. The output is significantly faster, more time-saving, and meets the satisfaction of customers and data recipients.
In the future, ROTHENBERGER’s sales team will be more involved. In the Creator role, they will be able to generate data exports for customers and initiate automated updates without requiring technical knowledge.
ROTHENBERGER’s assessment of working with nexoma
“From our perspective, nexoma has led the project very well. Priorities were set jointly from the beginning and implemented accordingly. nexoma has always responded promptly to individual requests, which were incorporated into the project. The management and implementation were truly excellent.
We are very pleased that this is not a typical client-service provider relationship. Instead, we have a partnership-based communication with very direct and immediate feedback from nexoma. This is exactly how we envision and expect such a collaboration.”
Bastian Seib, Head of Product Data Management / Head of Marketing Technology at ROTHENBERGER Werkzeuge GmbH
Technologies / data standards
- CatalogExpress
- Contentserv
- EXCEL
- CSV
- BMEcat
- ETIM
- FAB-DIS
- automated data-provision